Maintenance Planning Optimization for Airlines
Maintenance Planning Optimization for Airlines
Maintenance Planning Optimization for Airlines
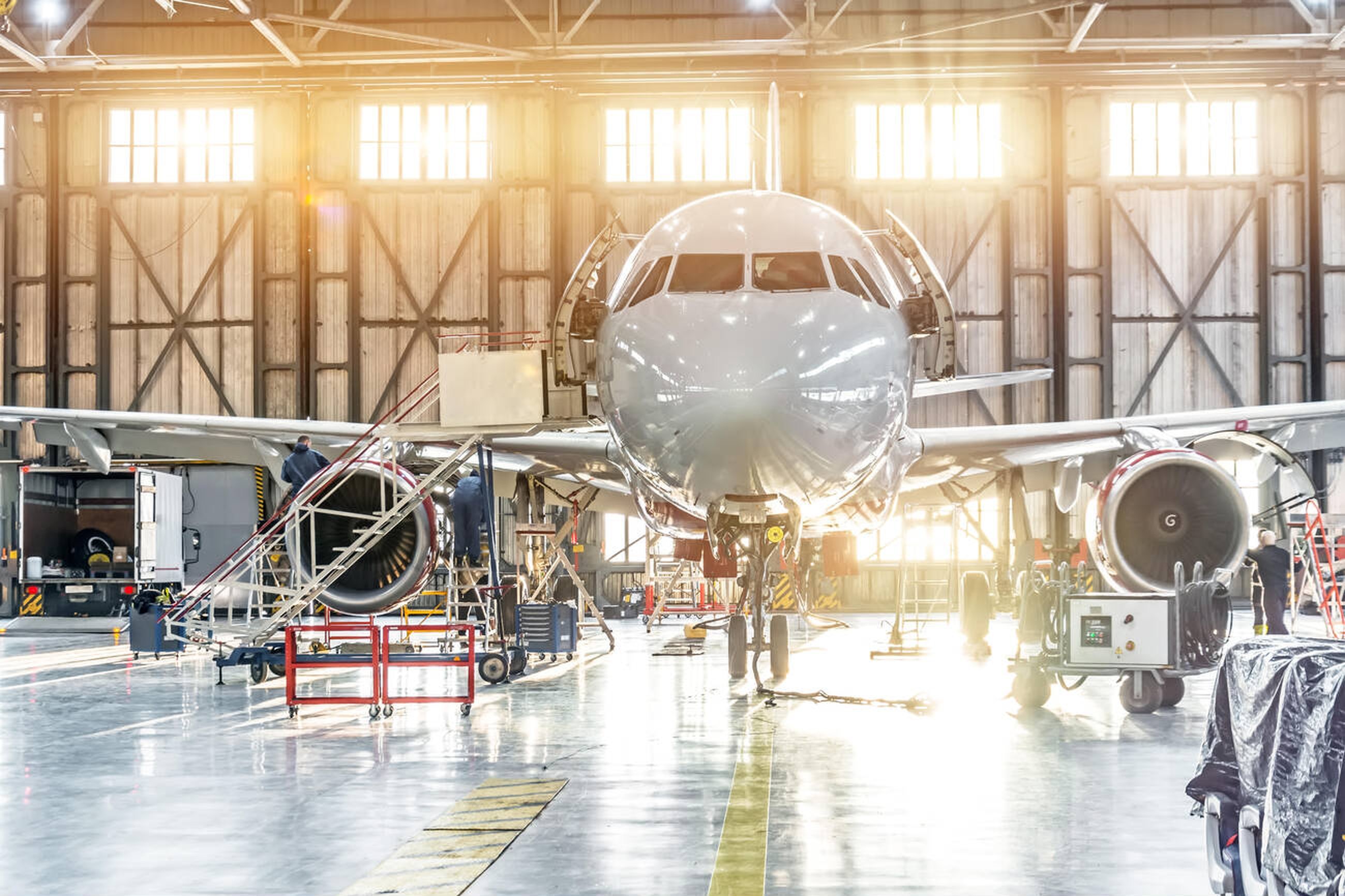
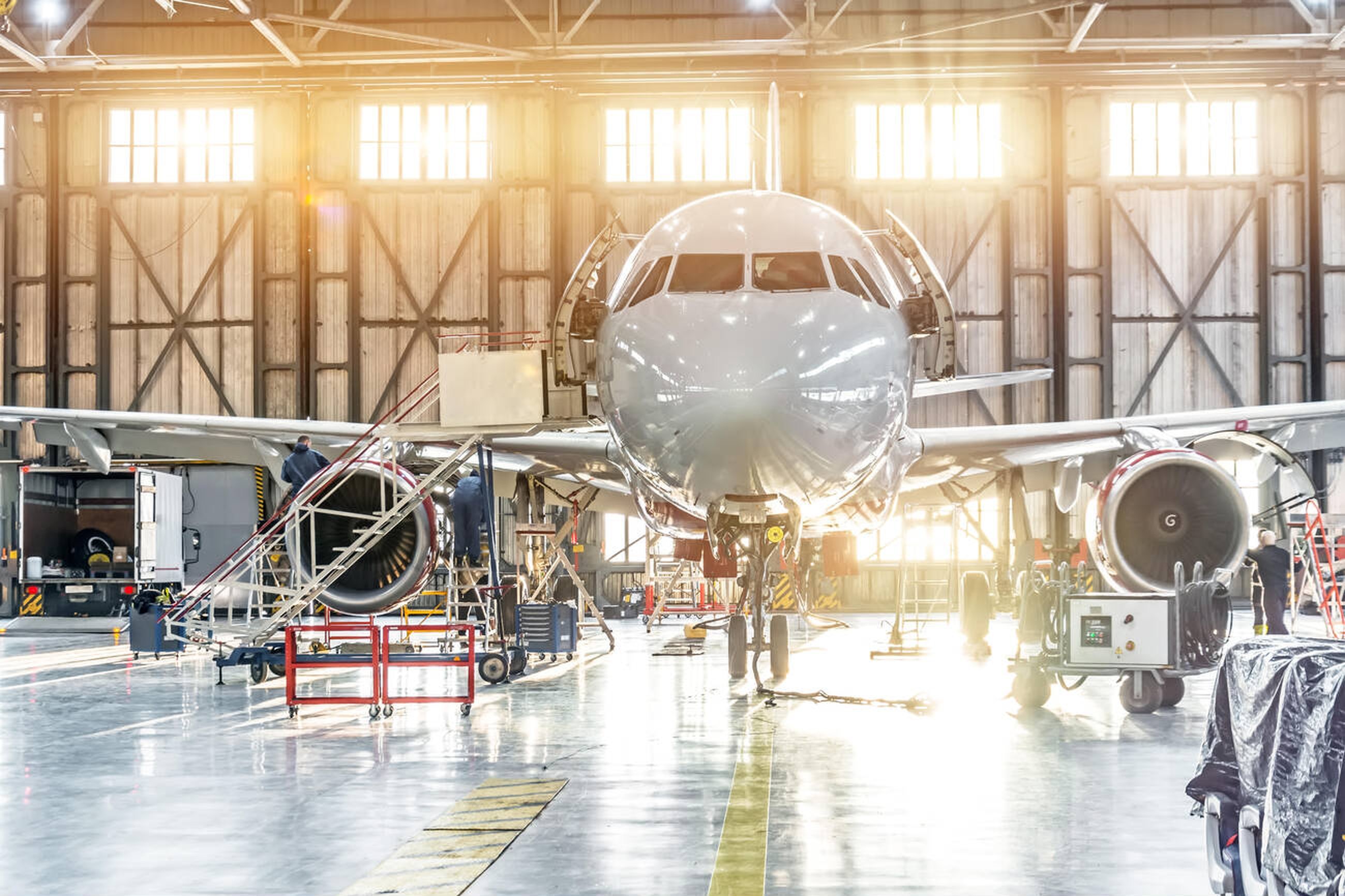
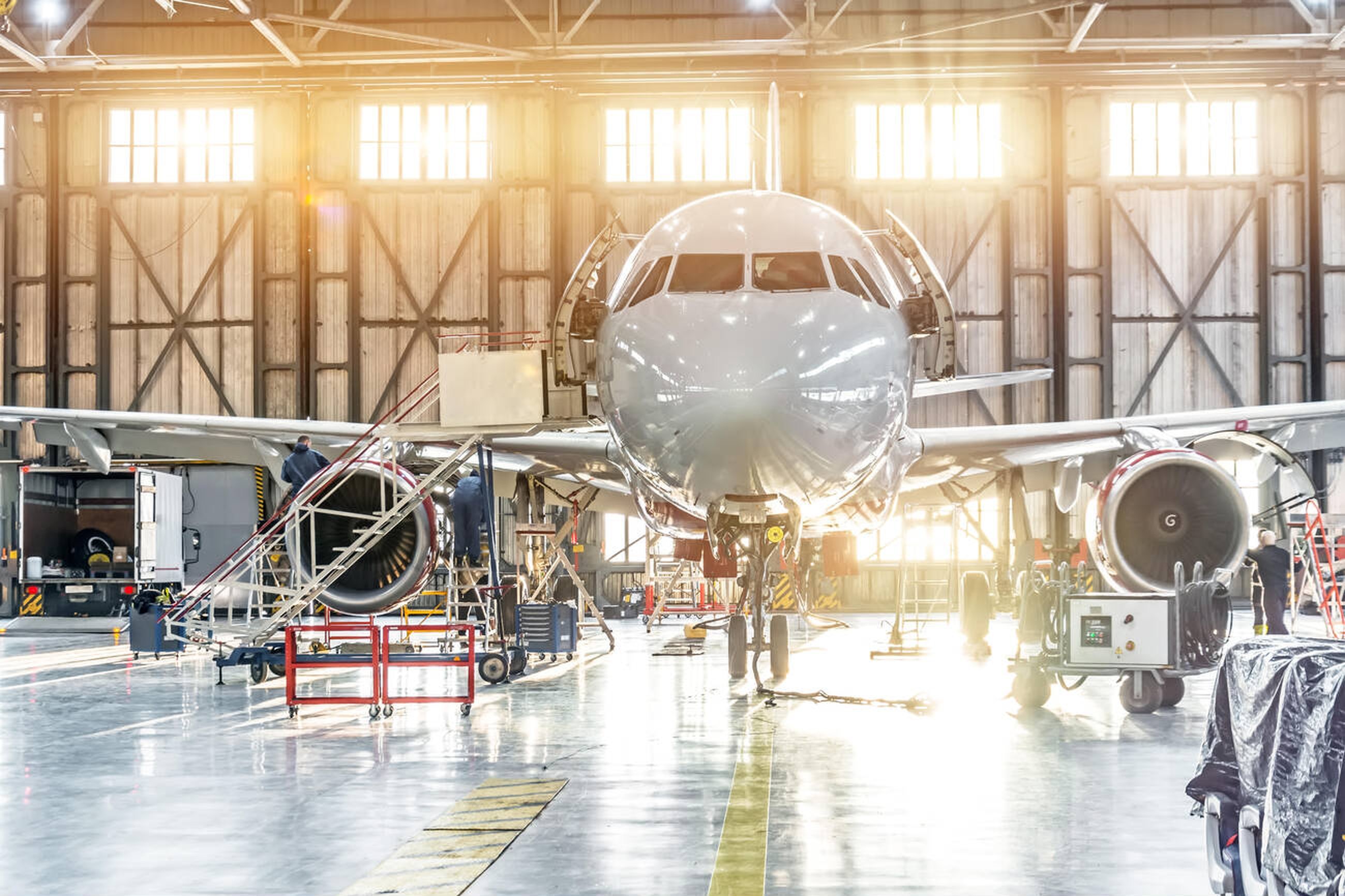
To optimize maintenance scheduling and minimize costs while ensuring full compliance with regulatory requirements and restrictions.
To optimize maintenance scheduling and minimize costs while ensuring full compliance with regulatory requirements and restrictions.
Airlines face complex challenges in efficiently scheduling aircraft maintenance while minimizing costs and adhering to strict compliance requirements. Traditional manual scheduling methods often struggle to balance conflicting objectives and constraints, leading to suboptimal outcomes. This case study explores the implementation of an automated maintenance planning optimization system to replace manual processes, considering a wide range of constraints, and improve overall operational efficiency for scheduling heavy, light, and line checks.
Airlines face complex challenges in efficiently scheduling aircraft maintenance while minimizing costs and adhering to strict compliance requirements. Traditional manual scheduling methods often struggle to balance conflicting objectives and constraints, leading to suboptimal outcomes. This case study explores the implementation of an automated maintenance planning optimization system to replace manual processes, considering a wide range of constraints, and improve overall operational efficiency for scheduling heavy, light, and line checks.
Airlines face complex challenges in efficiently scheduling aircraft maintenance while minimizing costs and adhering to strict compliance requirements. Traditional manual scheduling methods often struggle to balance conflicting objectives and constraints, leading to suboptimal outcomes. This case study explores the implementation of an automated maintenance planning optimization system to replace manual processes, considering a wide range of constraints, and improve overall operational efficiency for scheduling heavy, light, and line checks.
Results
Results
Replaced manual scheduling process with an automated, optimized solution.
Created cost-optimized maintenance schedules.
Ensured full compliance with regulatory requirements.
Improved utilization of manpower and maintenance bays.
Reduced overall maintenance costs Enhanced ability to handle schedule disruptions and changes.
Replaced manual scheduling process with an automated, optimized solution.
Created cost-optimized maintenance schedules.
Ensured full compliance with regulatory requirements.
Improved utilization of manpower and maintenance bays.
Reduced overall maintenance costs Enhanced ability to handle schedule disruptions and changes.
The implementation process began with a thorough analysis of the airline's existing manual scheduling process and its limitations. The team then formulated a Mixed Integer Programming (MIP) model that captured all relevant constraints and objectives. This mathematical model was designed to minimize maintenance costs while strictly adhering to compliance requirements.
The team worked on data integration, ensuring that all necessary inputs - such as flight schedules, aircraft details, maintenance requirements, personnel rosters, and facility information - were properly formatted and fed into the model.
The model incorporated commercial constraints to restrict the number of aircrafts that can be grounded simultaneously. Manpower availability was carefully modeled, taking into account shift patterns, skill levels, and certifications of maintenance personnel. Bay availability constraints were included to respect the physical limitations of maintenance facilities. The model also tracked elapsed flying hours for each aircraft, scheduling maintenance checks at the optimal time to balance cost and compliance.
The implementation process began with a thorough analysis of the airline's existing manual scheduling process and its limitations. The team then formulated a Mixed Integer Programming (MIP) model that captured all relevant constraints and objectives. This mathematical model was designed to minimize maintenance costs while strictly adhering to compliance requirements.
The team worked on data integration, ensuring that all necessary inputs - such as flight schedules, aircraft details, maintenance requirements, personnel rosters, and facility information - were properly formatted and fed into the model.
The model incorporated commercial constraints to restrict the number of aircrafts that can be grounded simultaneously. Manpower availability was carefully modeled, taking into account shift patterns, skill levels, and certifications of maintenance personnel. Bay availability constraints were included to respect the physical limitations of maintenance facilities. The model also tracked elapsed flying hours for each aircraft, scheduling maintenance checks at the optimal time to balance cost and compliance.
The implementation process began with a thorough analysis of the airline's existing manual scheduling process and its limitations. The team then formulated a Mixed Integer Programming (MIP) model that captured all relevant constraints and objectives. This mathematical model was designed to minimize maintenance costs while strictly adhering to compliance requirements.
The team worked on data integration, ensuring that all necessary inputs - such as flight schedules, aircraft details, maintenance requirements, personnel rosters, and facility information - were properly formatted and fed into the model.
The model incorporated commercial constraints to restrict the number of aircrafts that can be grounded simultaneously. Manpower availability was carefully modeled, taking into account shift patterns, skill levels, and certifications of maintenance personnel. Bay availability constraints were included to respect the physical limitations of maintenance facilities. The model also tracked elapsed flying hours for each aircraft, scheduling maintenance checks at the optimal time to balance cost and compliance.
Solution
Solution
A Mixed Integer Programming model was developed and solved using IBM ILOG CPLEX optimizer to generate optimal maintenance schedules that met all specified constraints and objectives.
A Mixed Integer Programming model was developed and solved using IBM ILOG CPLEX optimizer to generate optimal maintenance schedules that met all specified constraints and objectives.
The optimization model had to account for several key constraints to ensure feasible and efficient maintenance schedules.
Commercial constraints, which dictate the number of aircraft that can be grounded for maintenance, were considered to minimize the impact on revenue. Skilled maintenance manpower availability was crucial, ensuring that skilled technicians were available for each maintenance task. Bay availability had to be considered, as maintenance facilities have limited capacity. Elapsed flying hours for each aircraft were also a critical constraint, determining when maintenance was due and ensuring that aircraft undergo maintenance checks within specified time intervals. These constraints needed to be carefully balanced to create a schedule that was both compliant and cost-effective.
The optimization model had to account for several key constraints to ensure feasible and efficient maintenance schedules.
Commercial constraints, which dictate the number of aircraft that can be grounded for maintenance, were considered to minimize the impact on revenue. Skilled maintenance manpower availability was crucial, ensuring that skilled technicians were available for each maintenance task. Bay availability had to be considered, as maintenance facilities have limited capacity. Elapsed flying hours for each aircraft were also a critical constraint, determining when maintenance was due and ensuring that aircraft undergo maintenance checks within specified time intervals. These constraints needed to be carefully balanced to create a schedule that was both compliant and cost-effective.
The optimization model had to account for several key constraints to ensure feasible and efficient maintenance schedules.
Commercial constraints, which dictate the number of aircraft that can be grounded for maintenance, were considered to minimize the impact on revenue. Skilled maintenance manpower availability was crucial, ensuring that skilled technicians were available for each maintenance task. Bay availability had to be considered, as maintenance facilities have limited capacity. Elapsed flying hours for each aircraft were also a critical constraint, determining when maintenance was due and ensuring that aircraft undergo maintenance checks within specified time intervals. These constraints needed to be carefully balanced to create a schedule that was both compliant and cost-effective.
Benefits
Benefits
Significant time savings in maintenance planning and scheduling process.
Improved operational efficiency and resource utilization; saving maintenance costs.
Better adherence to regulatory compliance requirements.
Increased flexibility in responding to changing operational conditions.
Improved overall reliability and safety of aircraft fleet.
Significant time savings in maintenance planning and scheduling process.
Improved operational efficiency and resource utilization; saving maintenance costs.
Better adherence to regulatory compliance requirements.
Increased flexibility in responding to changing operational conditions.
Improved overall reliability and safety of aircraft fleet.
By implementing an optimized maintenance planning model, the airline achieved significant cost savings through reduced maintenance expenses. The model also enhanced operational efficiency by maximizing manpower and resource utilization. Reliability and safety of aircraft operations were bolstered, ensuring consistent performance. Additionally, the solution facilitated data-driven decision-making, empowering informed strategies for maintenance planning. This comprehensive approach delivered measurable benefits in cost, efficiency, and reliability.
By implementing an optimized maintenance planning model, the airline achieved significant cost savings through reduced maintenance expenses. The model also enhanced operational efficiency by maximizing manpower and resource utilization. Reliability and safety of aircraft operations were bolstered, ensuring consistent performance. Additionally, the solution facilitated data-driven decision-making, empowering informed strategies for maintenance planning. This comprehensive approach delivered measurable benefits in cost, efficiency, and reliability.
By implementing an optimized maintenance planning model, the airline achieved significant cost savings through reduced maintenance expenses. The model also enhanced operational efficiency by maximizing manpower and resource utilization. Reliability and safety of aircraft operations were bolstered, ensuring consistent performance. Additionally, the solution facilitated data-driven decision-making, empowering informed strategies for maintenance planning. This comprehensive approach delivered measurable benefits in cost, efficiency, and reliability.
This case study demonstrates the power of optimization techniques to improve efficiency, reduce costs, and enhance operational reliability in the aviation industry.
By implementing a maintenance planning optimization system, the airline replaced manual processes with an automated, constraint-aware solution, resulting in significant cost efficiency, improved resource utilization, and enhanced regulatory compliance.
This MIP model can be adapted by other airlines to achieve similar benefits, ensuring better decision- making, resilience to disruptions, and a competitive edge in the industry.
Adaptable to various airlines, this model can yield similar benefits: reduced maintenance costs, improved resource use, and enhanced compliance. As the aviation industry evolves, such optimization tools will be essential for maintaining competitiveness, ensuring safety, and enhancing passenger value.
This case study demonstrates the power of optimization techniques to improve efficiency, reduce costs, and enhance operational reliability in the aviation industry.
By implementing a maintenance planning optimization system, the airline replaced manual processes with an automated, constraint-aware solution, resulting in significant cost efficiency, improved resource utilization, and enhanced regulatory compliance.
This MIP model can be adapted by other airlines to achieve similar benefits, ensuring better decision- making, resilience to disruptions, and a competitive edge in the industry.
Adaptable to various airlines, this model can yield similar benefits: reduced maintenance costs, improved resource use, and enhanced compliance. As the aviation industry evolves, such optimization tools will be essential for maintaining competitiveness, ensuring safety, and enhancing passenger value.
For more information, write to us at info@planoptimus.com